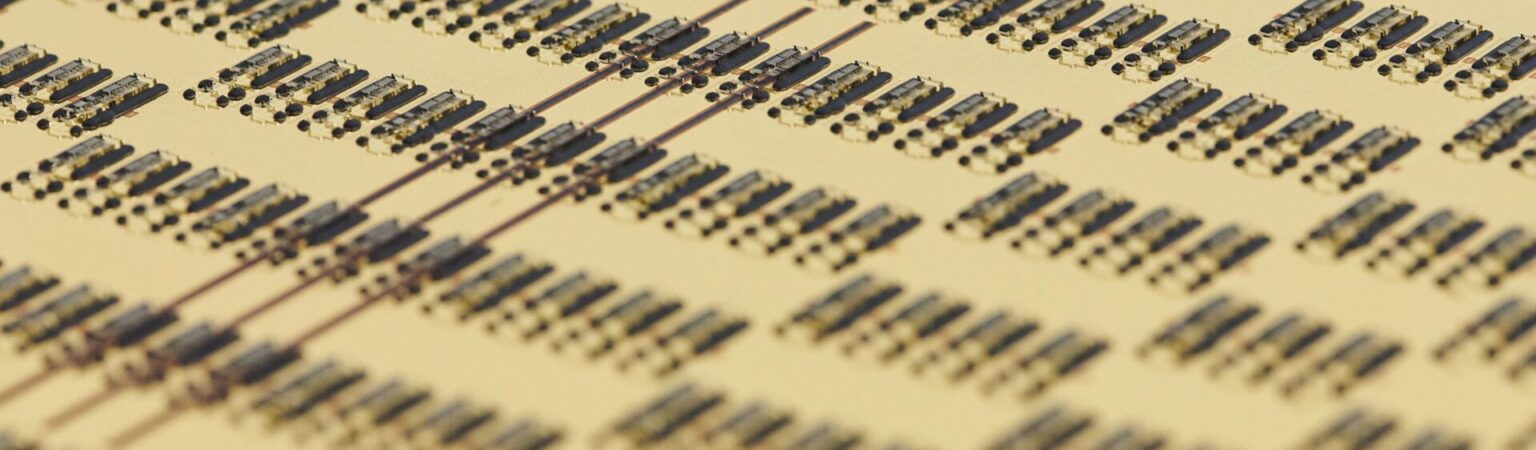
Member メンバー紹介
-
製品技術統括
Memory開発 技術開発H.M -
製品技術統括
Memory開発 製品設計S.T -
製品技術統括
Memory開発 技術開発U.K -
製品技術統括
基板設計 基板設計I.K -
製品技術統括
基板設計 基板開発O.Y
Prologue プロローグ
JEMが2010年頃から半導体装置(プローバー)メーカーと共同開発に取り組んだ「ML2」と、プローブカードメーカーと半導体デバイスメーカー、半導体装置メーカーの共同開発に当社が参加した「MLD」は、半導体のテストコストを削減するために、デバイスメーカーとプローバーメーカーとの共同プロジェクトにより開発した、新機軸のプローブカードだ。
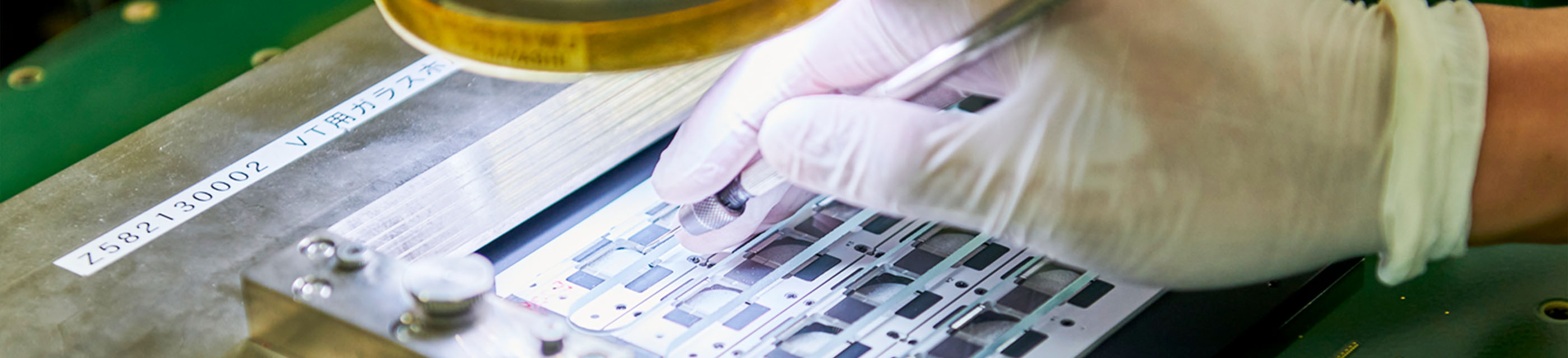
従来のテストでは、半導体ウエハ一つひとつにプローブカードをセットしてテストを行うが、本プロジェクトは複数の半導体ウエハを同時にテストできるプローバーを開発することで、トータルコストを大幅に削減することを目的としていた。
プローバーは複数のウエハをテストできる多段マルチセル構造。当社はこれに対応するプローブカードの開発を担った。
開発上の大きなポイントは、従来品のプローブカードに使われていた部品の大部分を、プローバー側のテストヘッドに配置したこと。一方のプローブカード側は極限まで簡素化し、基板とプローブ(針)、わずかな周辺部品のみの構造とすることで製造コスト(価格、工期)を大幅に削減することに成功した。
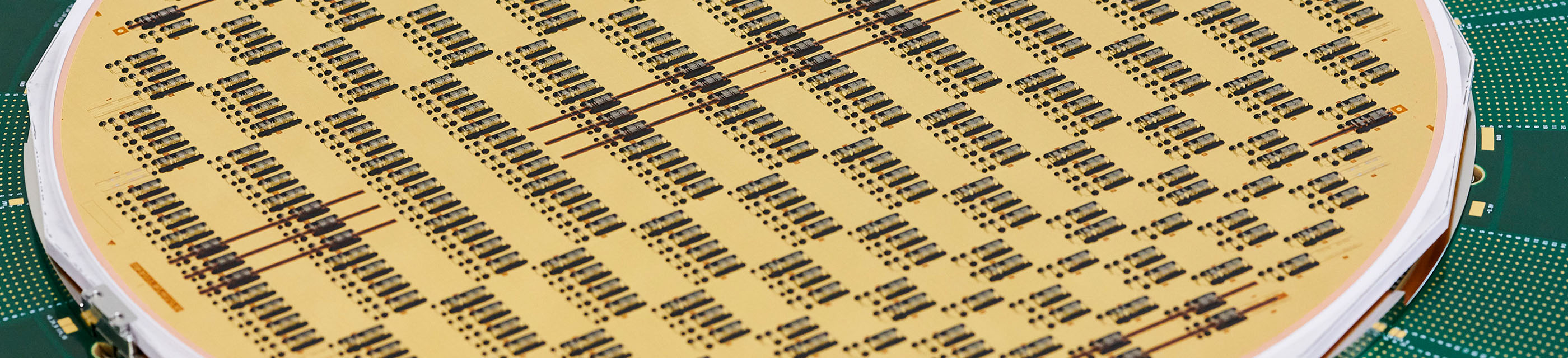
メモリカードなどに使われるNANDタイプ向けの「ML2」は、2015年の終わり頃に顧客の承認を得て量産を開始。売上全体の半分を占めることもあるなど、現在はJEMにおける主力製品となっている。
またPCなどの一時記憶、一次データ保管向けであるDRAMに対応する「MLD」も、2023年頃から量産を開始した。
今回はそんな一大プロジェクトに参加した多くのJEM社員の中から、5名のメンバーに話をうかがった。
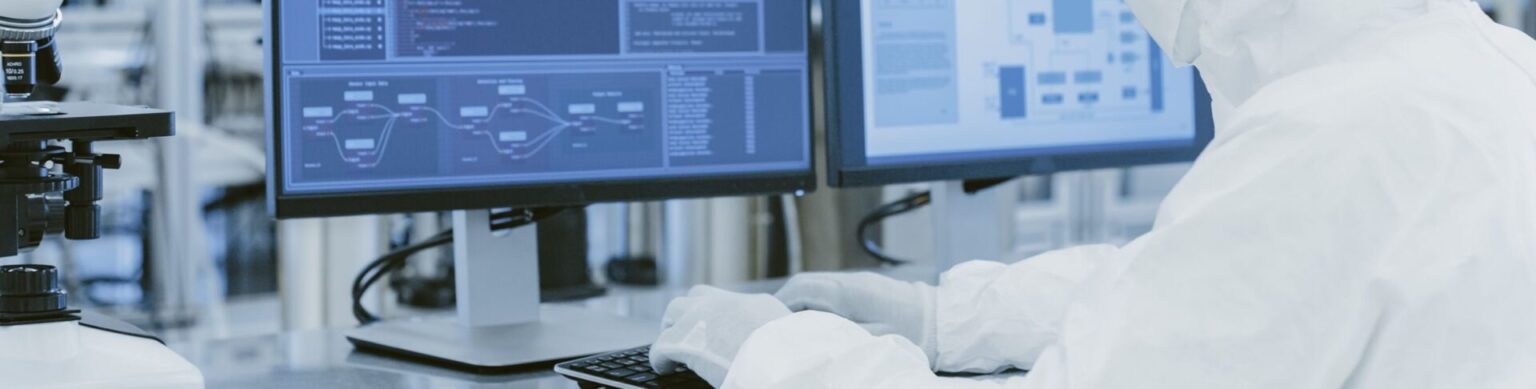
それぞれのスキルを活かして
-
「ML2」や「MLD」といったMシリーズは、そもそも2006年頃からはじめている「MC」がもとになっています。2009年頃から「MC」の量産がはじまり、その流れで「ML2」の開発がスタートしたんです。
私が担当したセラミック製基板(以下ST)という針を乗せる基板のデザインも、「MC」の流れを汲んだものです。 -
そうですね。私もH.Mさんと同じ機械的な設計を担当しましたが、私が入社した2011年当時にはすでに「ML2」の大まかな構造は決まっていたと思います。でも従来のプローブカードとは構造が大きく異なるので、プローブカード製造に関わる治具や出荷ケースなど、プローブカード以外の設計により多くの時間を費やしました。
-
私は開発が立ち上がった後の、量産のための機械設計業務を担当しました。主にプローブ(針)を並べていくデザインや構造体のデザイン、そして製造現場に対する指示書の作成も担当しました。
大規模プロジェクトだけに、設計だけでなく、お客様と製造現場をつなぐという点でも、大きな責任を感じながら仕事に取り組んでいました。 -
私とO.Yは基板設計部門に所属しており、私は電気的接続を担当しました。テスター・プローバー側に設置する針の場所や仕様はすでに決まっていましたから、プローブカード側の電気的接続をそこにどう落とし込むのかを考えました。「ML2」を経て、「MLD」の設計立ち上げに参加しています。
-
私は2018年の入社なので、「MLD」の開発の過渡期ぐらいからの参加です。「ML2」はNANDタイプ向けですが、「MLD」はDRAM向けです。その開発実績は当時の社内にもなかったため、試行錯誤しながら取り組んでいました。現在は当社の売上の柱となっており、新テスター向けの一部も承認中という状態まできています。
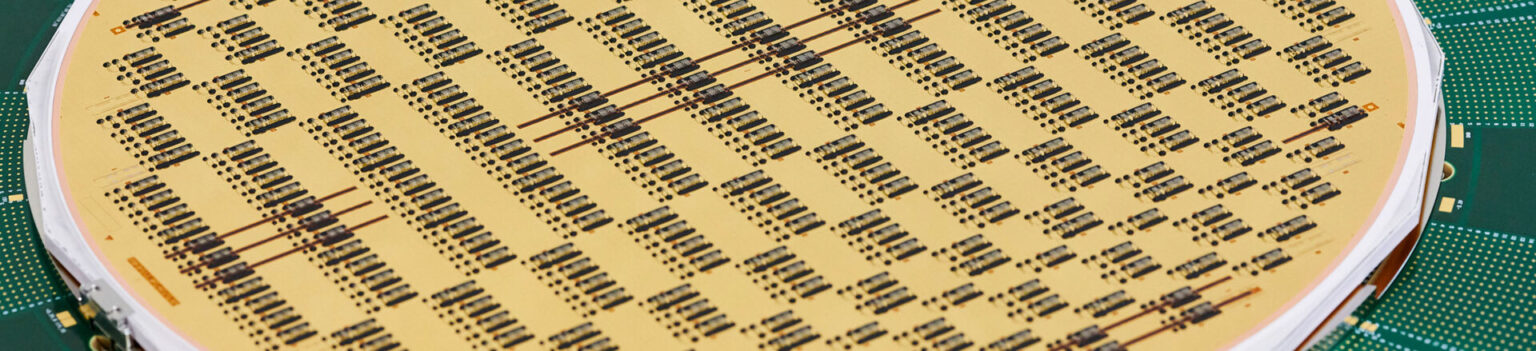
大規模プロジェクトならではの葛藤
-
私は、プローブカードは総合力が重要だと考えています。メカや電気といった技術に限らず、コストや納期、客先対応など、全てにおいて合格点をとらないと使っていただくことはできません。今回のプロジェクトでもそのあたりのバランスを意識しながら進めていきました。
特に開発の初期は当時の円高の影響などもあり、収益が見込みにくい環境でしたから、プロジェクトに関わるメンバーも多くはありませんでした。一人あたりの仕事が多い上に、私も別件で出張に出ることも多く、その分U.Kさんは大変だったと思います。 -
確かに大変でした(笑)。当時は「なんとかするしかない」「開発を遅らせることはできない」というプレッシャーをずっと感じていましたね。でもそのおかげで機械設計のスキルは大きく向上したと思っています。
個人的には、極限まで構造を簡素化するために、製造や搬送に必要なハンドリングする部分さえも省いたML2を、いかにハンドリングするかを考えることが難しかったと思います。プローブカードをプローバーに移すための治具の設計から、プローブカードを出荷する際に収納するケースまで、一から構造を設計しました。この部分に関してはお客様からの要求水準も高く、10回以上の試作を繰り返してようやく承認を得ることができました。 -
私はプローブ(針)のレイアウトのバランスに特に気を使いました。従来品であれば、プローバー(ウエハ)側がプローブカードに合わせて位置を調整してくれるのですが、「ML2」はプローバー(ウエハ)とプローブカードをコンタクトさせるシステムに最低限の機能しかないので、プローブカード側でプローブの位置を調整しなければなりません。
また、そのプローブのコンタクトの際には圧力が発生するのですが、その圧力が均衡になるような正確性が設計には求められます。これは非常に繊細な作業であり、ときにはパズルを解いているときに感じるひらめきも必要になる仕事でした。 -
「MLD」はDRAM向けなので、「ML2」に比べて配線密集度が高いんです。そのため客先から求められるスペックを満たしながら、決められた数の層の中でいかに結線を完了させるかが大きな課題でした。
-
確かに。「ML2」と「MLD」は基本的な構造は変わらないのですが、「MLD」はチップ1つあたりに使う配線の数が3~4倍になります。配線が互いに干渉しないように細心の注意が求められるので、毎回ぎりぎりのところを責めている感覚です。
-
そのように配線の難易度が高くなる一方で、納期はより短縮することが求められていますから、スピード感や効率もより問われるようになりました。
さらに、私たちの都合を優先して電気的設計をしてしまうと、後の基板部門の設計で困ることもあります。納期も含めて、いかに関係部門全体がつくりやすくなるのか、バランスを意識しながら取り組んでいます。 -
私たちの部門ではお客様と約1年にわたってやりとりを繰り返しました。毎週の打ち合わせで「もっとこうならないか?」と宿題をいただき、それをクリアしながらようやく承認をいただくところまでこぎ着けました。
時には求められている仕様に対して何度トライしても認めていただけず、辛く感じる時期もあったのですが、あきらめず地道に進めていきました。そうした粘りもあり、お客様からかなり大きな信頼が得られたと感じています。
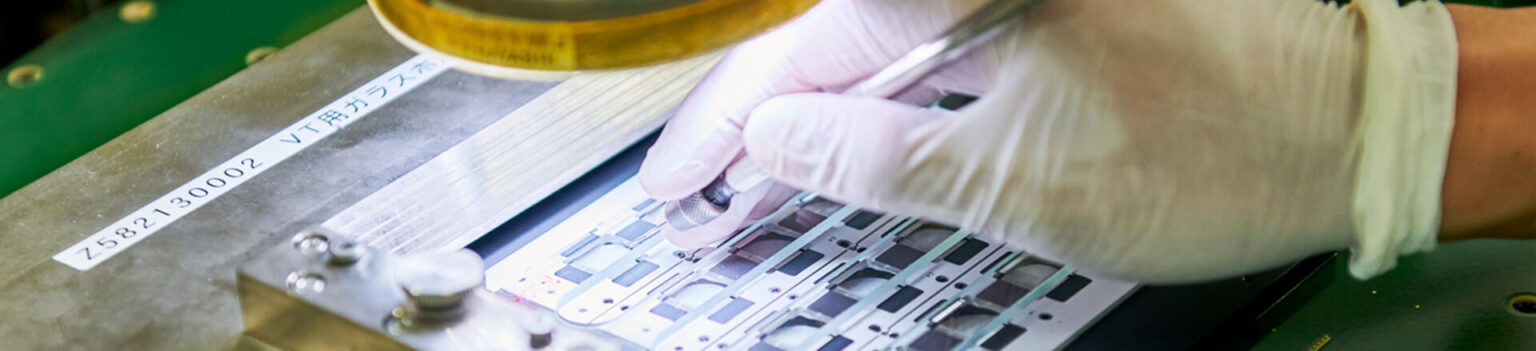
チャレンジを経て得たもの
-
「MLD」に関しては、プローバーの適切な位置にプローブ(針)をコンタクトさせるためには、理論計算が重要な意味をもっていました。参考にできるデータが少ない中での理論計算でしたから、正しい結果を導き出したときには、自分の計算力や想像力の高さが実感できました。
また、社内においても本プロジェクトへの貢献が認められて「社長賞」をいただくことができたことも、大きな喜びです。 -
私は異業種から転職したばかりの入社1年目からこのプロジェクトに携わりました。内容を理解するだけでも一苦労という状況から、自分なりに努力を重ねてプロジェクトの成功まで携われたことは、個人的な成長にもつながっています。もう一度同じ経験をしたいかと聞かれれば、なかなか「はい」とは言えませんが(笑)。
-
そうした苦労があって開発されたものを、量産化させることが私たちの使命でした。特に「ML」シリーズの生産規模はこれまでにないものであり、かなりの数を生産しなければ収益につながりません。原価を抑えつつ生産量も高めるという点では、このプロジェクトを経験することでより経営的な視点をもつことができたと思います。
-
技術面からいえば、電気的設計においては「MLD」のSTが、当社製品の中で最難関なんです。特性をより引き出す配置や配線が引き出しやすいレイアウトなど、これまで蓄積してきたノウハウを総動員してようやくクリアすることができ、自分の中でも大きな自信につながりましたね。
また、このプロジェクトを機に設計の自動化にも取り組みました。以前はGND配線という工程を5人がかりで作業していたところを、1人でもできるような自動化の仕組みが実現でき、会社全体にとっても大きな改善につながると思います。 -
私もU.Kさんと同じく、入社間もない頃にこのプロジェクトに関わることになりました。当時はそこまで大きなプロジェクトに参加しているという実感もなく、ただ目の前のことに必死に取り組んできましたが、今ではJEMの売上を指させる大黒柱になり、感慨深いものがあります。
私のケースのように、入社間もない人材にも、こうした大きな経験ができるところが、JEMの特長だと思います。半導体業界とともにJEMもまだまだ大きく発展していくと思うので、「仕事を通して大きなチャンスをものにしたい」という人には、ぜひ入社してほしいですね。